Rubber or materials with rubber-like properties are widely used for a great range of applications where the elastic properties of rubber are required. Since 3D printing with rubber was long not thought possible (rubber is a thermoset material), manufacturers started looking for a 3D printing alternative to rubber. The first one came through flexible PLA materials.
Nowadays, 3D printing with TPE and TPU is growing in popularity due to their great properties. But what is the difference between TPE and TPU?
TPE and TPU are thermoplastic elastomers, or rubber-like materials. They have been around since the 1950s. TPE’s and TPU’s are used to make rubber-like cases, lids, panels, soles for footwear, etc. Recently both materials became available as 3D printable materials for the additive manufacturing industry.
So what is the difference between the two materials? How do you decide for 3D printing in TPU or TPE? What is the difference compared to other types of rubber-like materials, like flexible PLA? Are TPU and TPE a good 3D printing alternative to rubber?
Difference between TPE and TPU
Before 3D printable TPE and TPU were available, the market looked at flex or soft PLAs to mimic the rubber-like qualities. But these are of lower quality in terms of wear and elastic properties than TPE and TPU. For industrial applications, there is no doubt that 3D printing with TPE or TPU offers much better results than with PLA. That is the main reason why FacFox does not offer these elastic PLAs.
When to choose for 3D printing with TPU over TPE and vice versa? We have already seen that TPU is a type of TPE. For that reason, it is safe to say that TPE is more common than TPU since it has been available as a 3D printing material for a longer period of time. TPU is a newer variant of 3D printable thermoplastic elastomers. When 3D printing with TPU you can expect your part to be firmer than the ones manufactured with TPE.
Thus, the real difference is not in the name but in available hardness grades. So your choice between TPU and TPE purely depends on the hardness that your 3D printed part requires.
TPE
Applications of TPE
TPE is used in the automotive and medical industries. But TPE can also be found in electronics as the cable jacket and around some headphone cables or any other application where rubber-like qualities are required.
3D Printing with TPE
TPE materials are available as filament for FDM and powder for use in SLS machines.
EOS already launched their TPE material for SLS in 2013 under the name of PrimePart ST (PEBA 2301).
CRP Technology offers TPE SLS-powder under the name: Windform® RL.
Also, Sintirit has TPE powder in their portfolio.
If you are looking for TPE filament: Roboze has a TPE filament in their portfolio called FLEX, for use in their Roboze FDM printers.
All of them are great options for engineers interested in 3D printing with TPE due to the outstanding quality of the printed parts.
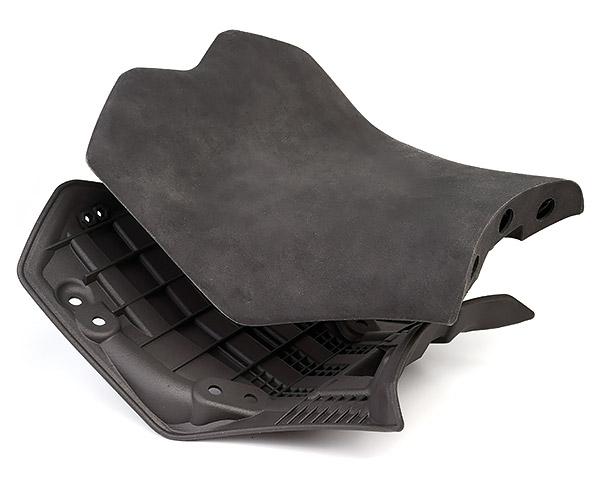
TPU
TPU than, stands for thermoplastic polyurethane and is a form of TPE or thermoplastic elastomer.
TPU was invented by BF Goodrich in 1959 (now operating under the name of Lubrizol Advanced Materials.) It is a thermoplastic elastomer belonging to the polyurethane class of plastics. TPU’s hardness can be customized resulting in material ranging from soft (rubber-like) to hard (rigid plastic). TPU comes in different colors as well as transparent. The surface can be smooth or rough to provide grip.
Applications of TPU
TPU can be found in many applications: automotive instrument panels, sporting goods, medical devices, soles of footwear, inflatable rubber rafts, mobile phone cases and TPU is the plastic around wire and cables.
3D Printing with TPU
TPU is available as filaments for use in FDM machines. TPU is a thermoplastic and is suitable for material extrusion processes: the material can be melted, cooled, and hardened.
TPU filament for FDM machines is offered by Stratasys as FDM TPU 92A. This material was introduced in November of 2018.
But 3D printing with TPU powders can also be done through SLS machines.
Polish material manufacturer offers TPU powders by the brand name FLEXA.
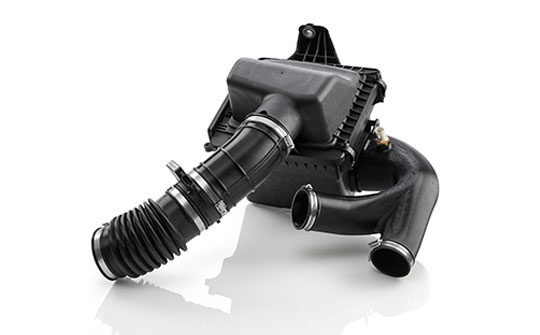
The German chemical and materials company BASF has a large portfolio of materials, among which a selection of TPU’s, branded under the name of Ellatollan, but it is only recently that they started offering TPU materials for additive manufacturing.
BASF is an ambitious new player in the field. BASF moved into AM in 2017 with the aim of building a portfolio of high-quality materials for additive manufacturing. They created a subsidiary, BASF 3D Printing Solutions GmbH, dedicated to additive manufacturing that will initially focus on the automotive, aerospace and consumer goods sectors. BASF is rapidly becoming a reference by providing outstanding materials for 3D printing with TPU.
Their rapidly growing material portfolio for AM includes: filaments (Ultrafuse and Innofil3D) and powders (Ultrasint and Adsint) and Advanced Photopolymers and Inks (Ultracur3D).
Their additive manufacturing portfolio has two TPU powders. One, Adsint TPU 90 flex, designed for Selective Laser Sintering (SLS) technology the other UtrasintTM TPU01 for HP Multi Jet Fusion printers. The materials were developed by Advanc3D Materials, a company acquired by BASF in 2018.
Adsint TPU 90 flex (thermoplastic Polyurethane) is a powder developed for SLS printing technology. Parts printed with Adsint TPU 90 flex have high elongation, excellent physical properties, rubber-like elasticity and good abrasive and chemical resistance. Typical applications are hard-soft systems, sport footwear, orthopedic models, hoses and tubes, sealings and wheels. BASF claims Adsint TPU 90 flex has been tested on most common SLS printers and can be used on machines of all sizes.
UltrasintTM TPU01 is the second TPU material in the additive manufacturing materials portfolio of BASF. This material is suited for use in HP Multi Jet Fusion printer.
New kid on the block: Silicone Printing
TPE and TPU are rubber-like plastic materials, and already of better quality the rubber-like PLA. But what about rubber itself? Printing with rubber itself was long thought not possible, because it is a thermoset material, but recently 3D printing in silicone, a rubber-type material has become available. Read the article Is 3D printing with silicone possible? to learn more about it.
Silicone printing, compared to printing with TPU and TPE, has much better elastic qualities and feels more like rubber, than the rubber-like materials that feel more like plastic. It is more expensive, but depending on your needs and requirements a very interesting option to consider.
Conclusion
TPE and TPU, both inventions of the 1950s have a wide range of applications and are widely used in the manufacturing industry, where rubber-like properties are required. Recently they have become available as 3D printing materials, as a better alternative to the previously available flexible PLA’s. Both TPE’s and TPU’s are offered at FacFox.